Organizational Agility, Keeping it Lean
Lean and agile can work alone but can be very powerful together.
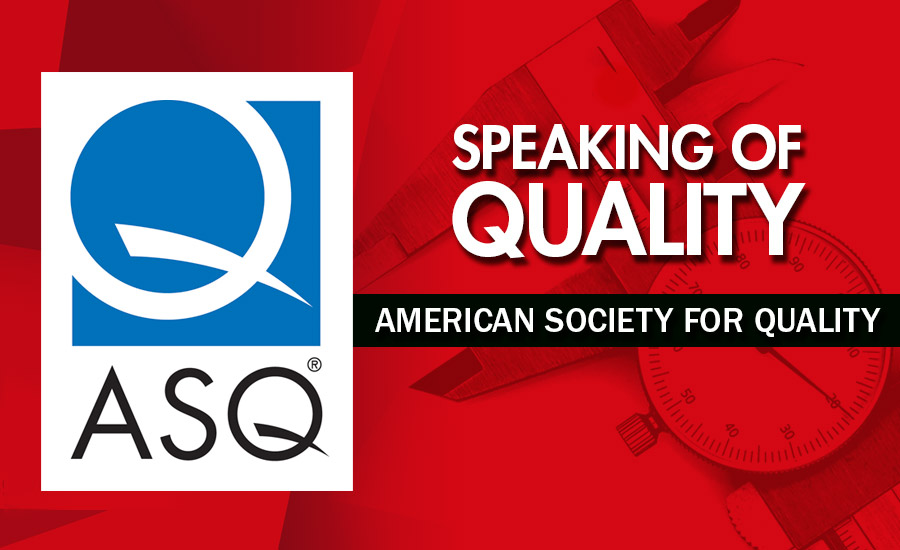
Lean and agile are well recognized in the manufacturing sector and in the quality community. Like many quality methodologies, lean and agile work in tandem and separately, depending on an organization’s needs. Where do these methodologies meet and diverge, what are their driving principles, and how you can add them to your toolbox (or convince others to do so)?
Lean dates back to the early 20th century and Henry Ford, with his famous assembly lines and his ability to turn over inventory in days. With just-in-time delivery, lean management, and lean thinking, lean went from shop-floor process to mainstream phenomenon. Through it all, the goal of lean was clear: zero waste. An essential aspect of the lean methodology is 5S.
5S is defined as a methodology that results in a clean, uncluttered, safe, and well organized workplace. The 5S quality tool is derived from five Japanese terms beginning with the letter “s” used to create a workplace suited for visual control and lean production. The pillars of 5S are listed below (with the English equivalent):
Seiri (sort): to separate needed tools, parts, and instructions from unneeded materials and to remove the unneeded ones.
Seiton (set in order): to neatly arrange and identify parts and tools for ease of use.
Seiso (shine): to conduct a cleanup campaign.
Seiketsu (standardize): to conduct seiri, seiton, and seiso daily to maintain a workplace in perfect condition.
Shitsuke (sustain): to form the habit of always following the first four S’s.
Benefits to be derived from implementing a lean 5S program include: improved safety, higher equipment availability, lower defect rates, reduced costs, increased production agility and flexibility, improved employee morale, better asset utilization, and enhanced enterprise image.
Agile dates back to 1968 when Melvin E. Conway coined Conway’s Law (“Any organization that designs a system will inevitably produce a design whose structure is a copy of the organization’s communication structure.”). While the law had been viewed in theoretical terms, there is recent research suggesting practical uses for Conway’s Law.
In 2001, 17 software professionals developed the “Manifesto for Agile Software Development,” which defined four main values. Several of the group formed the Agile Alliance. Here is the brief manifesto, which can be found at www.agilealliance.org/agile101/the-agile-manifesto/:
We are uncovering better ways of developing software by doing it and helping others do it. Through this work we have come to value:
- Individuals and interactions over processes and tools
- Working software over comprehensive documentation
- Customer collaboration over contract negotiation
- Responding to change over following a plan
That is, while there is value in the items on the right, we value the items on the left more.
The manifesto is supported by 12 principles
(www.agilealliance.org/agile101/12-principles-behind-the-agile-manifesto/). These principles point users on a steady course to something lean could never supply: variety. As stated above, agile began in software development but found a home in other sectors because agile enabled organizations to work quickly and effectively to meet changing customer requirements. Agile manufacturing focuses on a rapid response to customers, which can be used—like the lean organization—as a competitive advantage. Being agile puts your organization in a better position to take advantage of short windows of opportunity. With customer demands changing rapidly, those opportunities are becoming prevalent. There are four key elements for agile manufacturing:
- Modular product design (designing products in a fashion that enables them to serve as platforms for fast and easy variation)
- Information technology (automating the rapid dissemination of information throughout the company)
- Corporate partners (creating virtual short-term alliances)
- Knowledge culture (investing in employee training)
Lean and agile can work alone but they can be very powerful together. Reducing waste keeps your company sustainable. Being agile keeps your company ahead of the competition.
Looking for a reprint of this article?
From high-res PDFs to custom plaques, order your copy today!