Depth Steps on Gages
Avoid some common pitfalls.
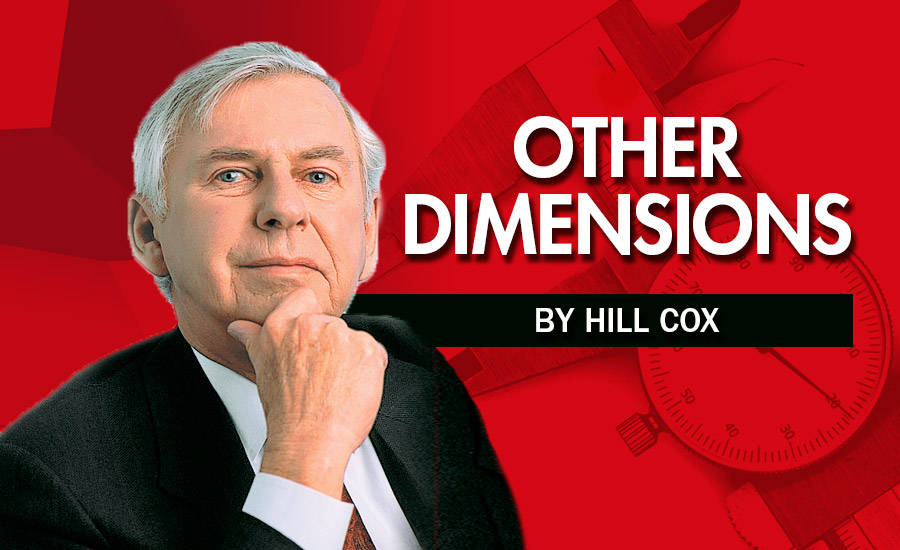
This is an area of gage making that takes something simple like a go/nogo plain plug gage and adds another feature for another check, such as hole depth. It can be a good cost saving idea; after all, the plug gage is already in the hole so a quick glance by the gage user enables this feature to be checked. But sometimes user expectations will not be realized because the feature and the gage to be modified to handle them are unrealistic or one cannot support the other. The following comments may help you avoid these pitfalls.
The first thing you have to determine is whether the plug gage member is long enough to contain depth steps, flats, notches or whatever mod you need for the depth involved. Sounds obvious I know, but we quite often get orders for go/nogo plugs that are not long enough to accommodate the required depth steps. Check your gage supplier’s catalog for the standard length of the Go gage member since that is the only one you can put them on. Some folks overlook this and ask us to put a flat for the Go length on the Go diameter and the flat for the Nogo length on the Nogo diameter member. Some diplomacy is required when we advise them that both have to go on the Go member since the Nogo member usually should not be going in the hole.
You may need an extra-long Go member to do this which is not a big deal but it will mean a special blank which means a higher cost for the basic diameter gage.
When you start butchering plug gage members for flats, whistle stops or other depth control features you have to consider the basic diameter of the gage. I have seen a gage that was too small a diameter with flats ground on it so deep that half the diameter was ground away and one part of the member was ready to break off the other. You should think very carefully about asking for flats on gages smaller than .150” or 3.8m in diameter. There are alternative methods to accommodate small diameters but this would require talking with your gage maker. And most times you’ll be looking at a specially designed gage which will cost you more.
Another situation that can be of concern is asking for unrealistic tolerances on the depth steps. If you need depth steps better than a few thousands of an inch tolerance you better have a discussion with your gage supplier. You may find that this way of checking the depth will not be precise enough so you’ll have to consider a flush pin gage which will be easier to work.
It should be obvious but it is not always so. If the hole being checked has a large chamfer or burrs from machining at the mouth of it, someone with the eyes of a hawk will be needed to do the check.
The tolerance on your Go plug gage member also has to be considered as that will determine whether the flats can be ground on the gage after the gage diameter has been finished. Close tolerance diameters are not as easily finished to size if the surface involved is interrupted by flats which can make lapping of it a problem. If flats are going on a finished gage it has to be carefully and slowly done to avoid messing up the diameter and keep in mind that the gage may be case hardened rather than through hardened.
Thread plug gages often have depth steps on them so all of foregoing comments apply plus one other. Do you want the steps to indicate the depth from the end of the gage or from the first full form of the thread on that gage? The difference between the two will be equal to the pitch of the thread which can be significant.
Now it was not my purpose to shoot down your quick depth check idea, but you should be aware of what can go wrong. If I haven’t made it clear enough by now, a discussion with the people who will be making the gage is your first step to getting what you want—if it’s possible.
Looking for a reprint of this article?
From high-res PDFs to custom plaques, order your copy today!