Measurement Management & the Applicable Standards
Inspection depends on well-defined measurement processes.
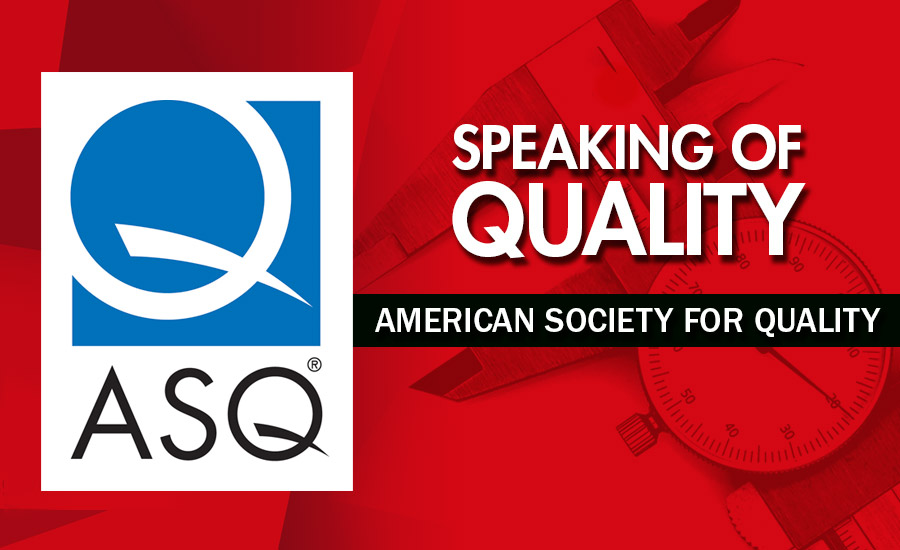
Many times, in the world of quality, there are resources available that are unknown to many of our colleagues. One of these resources is the standard ISO 10012: 2003, “Measurement management—Requirements for measurement processes and measuring equipment.” The current version is written to supplement ISO9001: 2008. This does not detract from its importance or relevance to ISO9001: 2015 and quality in general. This international standard also supplements the requirements of ISO/IEC 17025, which “specifies the general requirements for the competence, impartiality and consistent operation of laboratories.” (iso.org)
Having management involvement is critical for the metrological function to properly provide inspection and test with the resources required to assess conformity to customer requirements. The management responsibility clause addresses the metrological function and customer for this purpose. There is also a requirement to include the managements of metrological functions as a quality objective and management review within the quality management system (QMS).
Competence is a critical requirement for employees involved in metrological functions as well as for test and inspection. Interdependence and interrelationship between employees who perform these functions and activities is essential to have valid and reliable results.
Inspection depends on having well defined measurement processes. ISO 10012 provides organizations requirements for creating and implementing measurement processes. Information resources is a key requirement which addresses procedures, software, records and identification. The measurement process also includes requirements for measurement process design, realization of the measurement process and records. Measurement uncertainty is required for each measurement process. This is essential to ensure the measurement system is reliable.
Measuring equipment utilized in test and inspection is the focus of the material resources clause. The subclauses of the standard include measuring equipment and environment. While reading through ISO 10012, I encountered a term that was new to me. The phrase was metrological confirmation. Within the standard, metrological confirmation is defined as, “designed and implemented to ensure that the metrological characteristics of the measuring equipment satisfy the metrological requirements for the measurement process. Metrological confirmation comprises measuring equipment calibration and measuring equipment verification.” Of course, records are essential for documented evidence.
The measurement system is so critical to an organization to have reliable and valid results it must be audited and monitored on an ongoing basis. Nonconforming work (or nonconformities, which include damage, malfunction and mishandling) is a risk and must be addressed with proper corrective action. As with any system, it is better to focus on a proactive approach (preventive action) than need to employ corrective action throughout the quality system.
In summary, the ISO 10012 standard assists an organization to include the critical area of measuring processes and equipment into the QMS. The ASQ Inspection Division, in conjunction with the Standard Committee, is composing a USA National Standard for Inspection which combines key points of ISO 10012 as well as inspection principles and devices.
Looking for a reprint of this article?
From high-res PDFs to custom plaques, order your copy today!