What Kind of Calibration Do You Want?
You want a functional calibration.
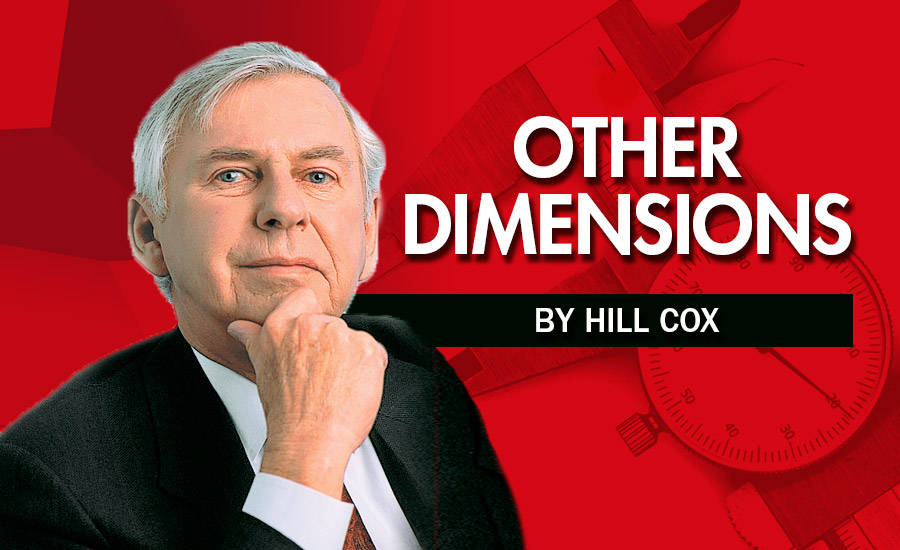
Typical answers include: cheaper, faster, most accurate, none of which would pass a technical smell test. On reflection, many might say they want calibration to tell them if the item to be calibrated is any good or not while not defining what ‘good’ means from a technical point of view.
Those who are unable or unwilling to make the call will usually revert to some technical standard or specification the item was ‘apparently’ made to and leave it up to the lab to take it from there. This can be a very expensive way to go and provide you with a lot of information you may not be able to use effectively. Such standards relate to instruments and gages when they were new so the tolerances in them are for the maker of them, not necessarily the user of them.
At the end of the day, most requirements can be grouped into ‘how good is it?’ That is what most users of these devices want to know. Armed with this information, they compare it to what they need, i.e. the tolerances of the items used to check or measure. To keep things simple, if this is your situation, what you want is a functional calibration to determine if the item involved is good enough for your work. If the device does not meet all critical criteria of a specification, it will show in the answer from the lab as to how precise it is.
In some cases, an instrument may not come close to the values outlined in a specification but is more than adequate for your needs. If you’ve requested your calibration source to calibrate it to a specification it could be rejected because of that requirement. Explaining to a quality auditor why it doesn’t matter can be a challenge so skip the new specs and ask for a functional calibration.
If your company uses a lot of ZZ tolerance pin gages as go/nogo gages they live in a world of their own that you should be aware of. They were never intended to be cheap substitutes for regular go/nogo gages and thus do not meet similar criteria. For example, regular go/nogo gages are expected to be within published specs for diameter over their length but the ZZ versions allow for approximately the first 1/4” from each end to be undersize and still considered satisfactory. Not a problem if you’re using them on through holes but useless for blind bore diameter checks. Ensure your calibration source knows this or you’ll end up with a lot of good, but rejected pins.
And speaking of ZZ tolerance pins in sets, there’s a good reason why they are so low in cost: volume. They are usually not inspected 100% for size for the same reasons many of the components they are used to check are not. And when they are, the lab doing the work is doing so on a one-off basis and are unable to amortize the setup costs over fifty or more pins of the same size. That is why they are cheaper to buy as new than to calibrate them.
When it comes to thread plug gages—you knew I’d get here sooner than later—if you ask for them calibrated in accordance with the standard they’ve been made to, the cost of doing so would be many times the price they cost to buy. This is due to the many elements involved that would have to be verified, some of which few labs have the capability of doing to the level of precision required. The default calibration is simple pitch diameter since wear will show up in that reading first, but other elements can be just as critical and make the functional size quite different than simple PD.
Most labs automatically default to simple PD when asked to calibrate thread plugs but if you’re having difficulties with thread inspection, you may need more detailed calibration at a higher cost.
And, as I’ve mentioned before, thread ring gage calibration is, by default, done by use of a setting plug gage. Direct measurement of adjustable thread ring gages will never produce a functional calibration of such gages so you should always stipulate that a setting plug to the appropriate ASME standard is used.
Looking for a reprint of this article?
From high-res PDFs to custom plaques, order your copy today!