Inspection in Quality 4.0
Digitization and automation will ensure better quality.
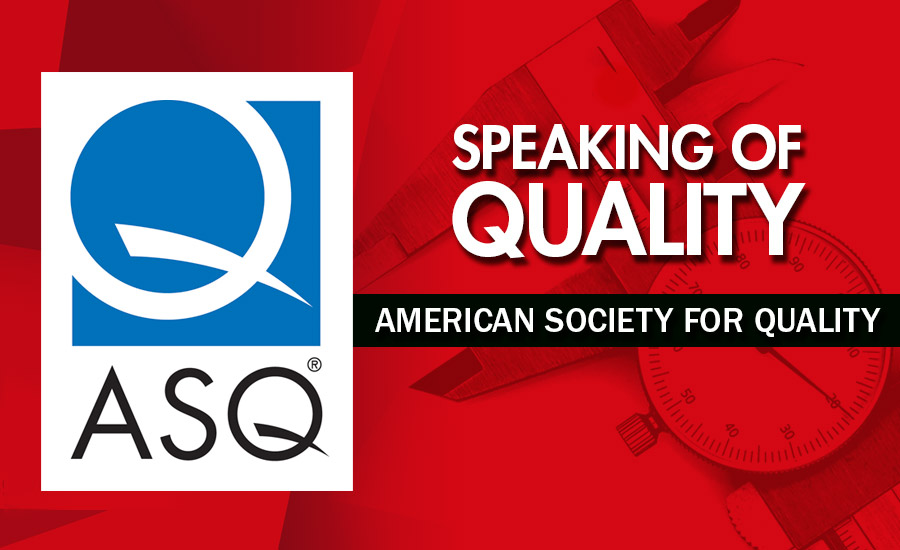
Today’s world has never been more dynamic, and it’s constantly changing at an accelerated rate by adopting more advanced technologies. Industry 4.0 refers to these accelerated changes to the way we live, work, and communicate. Industry 4.0, in its essence, describes the trend towards automation and data manipulation—mostly in the manufacturing environment—which include cyber-physical systems, the internet of things and systems, information and communications technology, new materials, big data, cloud and cognitive computing, augmented and virtual reality, artificial intelligence, and machine learning. Quality 4.0, a subset of Industry 4.0, integrates the features from Industry 4.0 with traditional quality tools and methodologies to achieve better operational excellence, overall performance, and innovation. Quality 4.0 combines people, processes, and technologies to accomplish these goals along with complete digitalization of quality management systems. It doesn’t substitute for traditional quality tools and methodologies, but rather builds and improves upon them.
In the light of these changes and new technologies, companies will rely more on automated systems to collect required data to be able to verify product and process conformance. These automated systems will include sophisticated sensors, robots with artificial intelligence capabilities, machines able to constantly learn, and other technologically advanced equipment to collect data from the manufacturing processes and then, using analytics, monitor process performance and take proactive measures if the processes start to deviate from the target. This equipment is designed to support the manufacturing processes with accurate data collection, producing more effective measurement, analysis, and control.
The ultimate goal of these changes is to enable manufacturing facilities to produce better products at lower cost and increase their adaptability by expediting their response to changes in demand, decreasing processing time, and achieving greater competitiveness.
Digitization and automation will ensure better quality and compliance by reducing manual errors and variability, as well as allowing faster and effective resolution of problems. Prevention of major compliance issues will lead to enormous savings related to the cost of poor quality. Furthermore, improved agility and shorter inspection time will reduce operational lead times and increase profitability. The inspection of operations and processes will occur in real time and ultimately increase efficiency of entire production systems. By using technologically advanced controlling systems that are embedded into production lines with high accuracy and precision, quality information related to products and processes will be constantly monitored. Therefore, the measurement system variation will be reduced, if not completely eliminated, so companies can focus on improving natural variation in their processes. The need for measurement system analysis could also be eliminated, since the technologically advanced equipment will be able to constantly repeat the same operations and obtain precise measurements by greatly improving measurement productivity. Therefore, gage repeatability and reproducibility analysis won’t be required since human subjectivity, inconsistent training, differences in operator skills, and instrument variability will be marginalized.
Considering all these incoming changes, the role of existing inspection will change as well. Since measuring of performed operations will be done by automated equipment built into the machines and production lines, inspectors will have to shift their role. Instead of performing measurements directly, inspectors will have to slowly move toward quality predictive analytical roles and focus on identification of deviation in observed processes and communication of identified trends. The inputs—such as where to place measuring equipment on the production line, when and how to collect data, and comprehensive reporting to support rapid decision making processes—will also become an important role of inspection in the future.
The changes coming with Quality 4.0 will affect the way we operate—and traditional inspection. With automated equipment built into production systems that will be capable of collecting data in real time with extremely high precision and accuracy, inspectors will need to shift toward more predictive quality analytical positions. Instead of direct participation in the measurement process, inspectors will play crucial roles in making decisions related to measuring processes, analyzing collected data, and taking appropriate preventive measures to improve existing processes.
Inspection and Quality 4.0
ASQ has many resources about inspection and Quality 4.0.
Inspection Division—Members of the technical community receive information about new inspection trends and information about networking opportunities. http://asq.org/inspect/.
Learn About Quality 4.0—This ASQ Quality Resources page includes general information about Quality 4.0 and links to white papers, research, webcasts, and other articles. asq.org/quality-resources/quality-4-0.
ASQ Quality 4.0 Summit—Visit asq.org/conferences/quality-4-0 for conference information.
ASQTV—Start watching now at https://videos.asq.org/product-category/channel/quality-4-0.
Looking for a reprint of this article?
From high-res PDFs to custom plaques, order your copy today!