When Everyone Disagrees: A Look at Method Points to Resolution
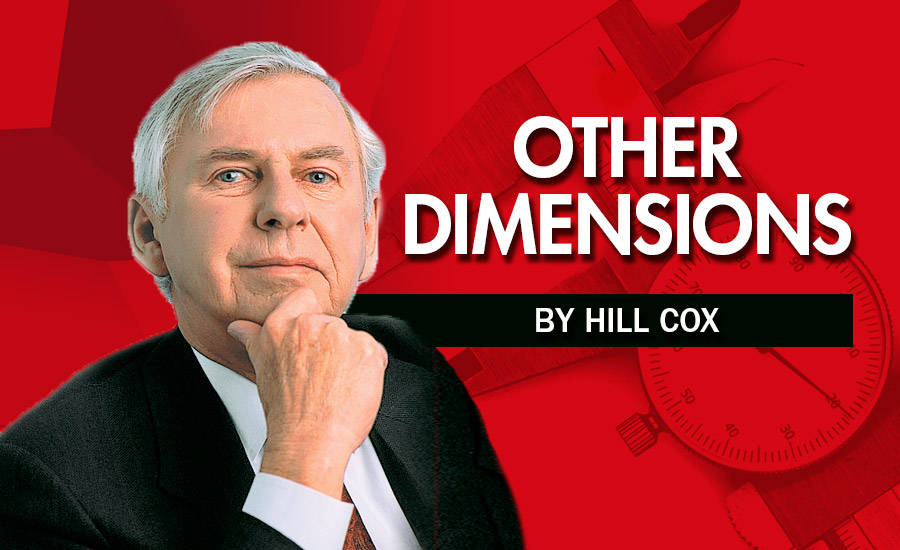
This situation pops up quite regularly when a relatively simple feature such as the diameter of a hole in a machined part doesn’t appear to be right when the part is at the assembly stage of manufacture. Like similar disputes, the finger pointing begins and compromises are made but the problem doesn’t go away. A fixed limit plug gage rejects the hole while direct measurements with various instruments says it’s okay so a coordinate measuring machine (CMM) is brought into the fray and its numbers disagree with those obtained by the other two methods. But since the CMM is a sophisticated device and a lot more expensive, there’s a tendency to believe what its readings imply compared to the lowly plug gage. The battle lines get shifted to a fight between how good each device is as opposed to how precisely each method provides values for the functional size of the hole, which is what the problem was in the first place.
A look at how each of the methods does what it is supposed to do is revealing and points the way to resolving the issues. My comments assume each device is calibrated and functioning well.
The plug gage is simply a ‘yes’ or ‘no’ answer to the size of the hole. If the hole has geometry problems, such as taper, straightness or out-of-round conditions of significant magnitude, the gage may reject it.
If the usual handheld instruments such as bore gages check the hole, conditions such as taper and ovality will be indicated by the readings if enough of them are taken to show this picture but if other out-of-round conditions such as 3-, 5-, or 7- point lobing is present, they will remain undetected but may have a significant effect on functional size. Should the hole be measured by 3-anvil bore measuring micrometers these conditions will be revealed but ovality, which is two or four-point lobing, will not.
The CMM will give much the same level of detail as handheld instruments and then some but only if the measuring routine for the machine is set up to do this. If the centerline of the hole is at an angle, standard diameter measurements taken by the CMM will not reveal this condition but it will influence each diameter reading taken unless the machine operator takes the necessary steps to square up the part or correct the diameter readings for the condition.
CMMs measure diameters by taking discrete readings about the periphery of the diameter, which the machine’s software then processes to give a diameter reading. The more points measured – which is usually part of the machine’s setup - the more closely the machine will get to the actual diameter. Similarly, if the machine is programmed to compare diameter readings to detect taper, etc., the more diameters measured the more chances of finding geometry problems and getting values for them.
The plug gage and handheld instruments are free to find the diameters they are measuring; they are not mechanically restrained like the CMM. However, if such a condition is detrimental to the hole function, the CMM will detect it or present diameter readings indicating it.
Sooner or later someone may suggest using an air gage to measure the hole considering such gages are known for high accuracy in this type of work. If you have the time to get the tooling made, which is size specific, it’s worth considering but there are some limitations you should be aware of. Since an air gage is a non-contact device, the surface finish of the bore being measured must be good enough as the air will average its readings between the peaks and valleys of the finish. The range of an air gage is usually much smaller than other instruments, which can limit their usefulness. And, to make matters more interesting, you’ll need to specify whether you want two or three-jet type plugs depending on what type of roundness problems you expect to crop up.
As you can see, different methods of measurement require interpretation to arrive at useful answers to resolve disputes. In the example I have been using, the lowly plug gage will not give all the information that other methods do but will reject the hole if any of the variations I’ve noted interfere with the functional size of the hole. Sometimes, simple answers are all you need.
Looking for a reprint of this article?
From high-res PDFs to custom plaques, order your copy today!