Speaking of Quality | Charles W. (Wes) Shelton
Measurement System Analysis More Than a Line on a PPAP Submission
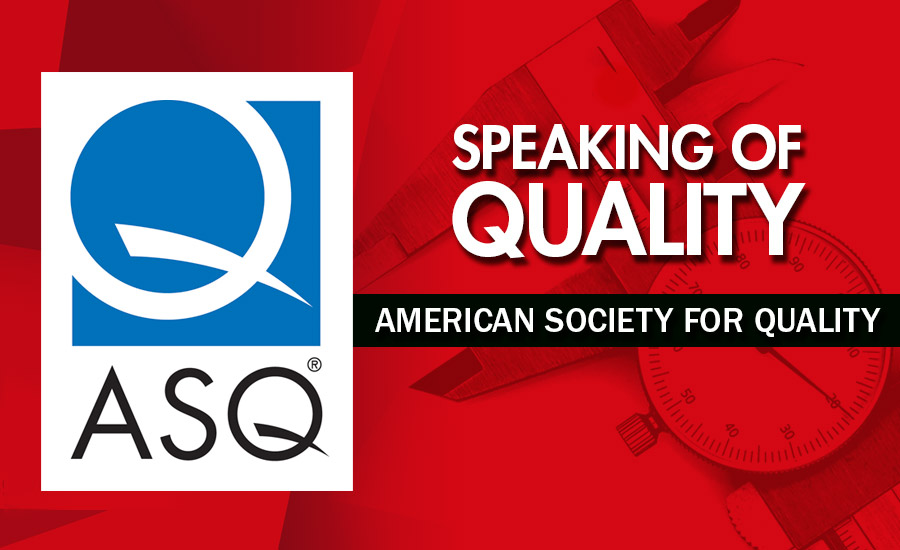
For those of us in the manufacturing world, measurements on products and processes are all important to ensure the products will meet customer requirements, perform correctly, safely, and for a reasonable lifespan. We place our faith in the measurements to accept or reject product—or to adjust the manufacturing process. But are the measurements correct—and how would we know? There is nothing to be gained by using a measurement process or gage that gives five different results when the same characteristic is measured five times!
In his book, “Economic Control of Quality of Manufactured Product,” published in 1931, Dr. W. A. Shewhart opens chapter 23 with these words, “In any program of control, we must start with observed data; yet the data may be either good, bad, or indifferent. Of what value is the theory of control if the observed data going into the theory are bad?” Dr. Shewhart recognized that poor data can lead to poor decisions. In the world of inspection, poor measurements can lead to poor decisions or results—products that do not conform to specifications or processes adjusted incorrectly, or that unintentionally escape to the end customer.
Enter Measurement System Analysis
You are probably already thinking that measurement system analysis (MSA), or “gage R&R,” is the answer to ensure good measurements. This process helps us to ensure that our measurement processes—whether for dimensional measurements or attribute assessments—are accurate, precise, and stable over time. We can conduct statistical studies of the instruments and their measurements to determine if the instruments can really determine an unbiased value of the characteristic and do it repeatedly, even when used by different operators or inspectors. Once we meet a threshold of acceptance, we begin to have some confidence that the gage can tell the difference between parts and its inherent variation. We perform the analysis, check the box, and submit the PPAP and all is right with the world. But is there more that can be achieved from the MSA process?
Can There Be More?
In one of my quality positions, the task was to improve the staging of a tool assembly for a compression molding machine that made bottle caps. There were 54 tool stations on the molding machine. Variation in the staging yielded variation in the caps from molding, the other downstream processes (such as scoring and lining), and finally, in the finished caps to the customer. This variation made the bottling process more difficult, thereby reducing the customer’s productivity. Simply put, variability in tool staging at the molding process yielded problems in cap manufacturing (internally) and at the bottler (externally).
Originally the staging was done with a manual process so designing a gage that could hold the assembly—which weighed several pounds—provided the correct staging pressure to simulate the tool in the machine. To determine the true length of the assembly accurately and precisely was quite a task. The original new design was created and while it seemed to be an improvement, the analysis told a different story. The design could not stage the tool’s reliability to within 0.001”. Initial analysis showed the new fixture used well over 100% of the staging tolerance in its variation.
The MSA gave us direction to look at the measurement process and the condition of the components in the assembly. One area of concern was that the shimming washers contained an exceedingly small burr that was crushed in use resulting in a changing length of the tool over time. Secondly, the structure of the new (and original) gage proved to be insufficient to withstand the forces in setting the pressure for measuring the tool. To resolve the shim issue, a change was made at the supplier to ensure burrs would not be present on the shims. The redesign of the staging fixture went from aluminum to steel components, an improved cradle to support the tool, improved pressure delivery, and gaging with finer resolution. The result was a measuring process that assured the tools were staged well within the 0.001” requirement—using less than 10% of the staging tolerance.
But The Rest Of The Story…
Improving the measurement of the tool staging process allowed for faster staging of the 54 tool stations and reduced cap variability from molder, which positively affected the process to the bottling customer. If that were all that was gained, that would have been successful. However, once word of this new staging fixture got out to the customers who purchased our molding equipment, there was an immediate demand for the fixture. The fixture was commercialized and sold, generating another source of revenue for our company, and providing improvements to others who manufactured caps for their bottling customers. Since the caps from the molder now had less variation, a new cap measurement system had to be designed to correctly measure the reduced variation caps. And yes, this too became another commercial product for the company, yielding yet another income stream.
While the quest for good measurement data inspired by Dr. Shewhart drives us to ensure our inspection data is good, more may be obtained from a measurement system study than simply accurate and reliable measurements. Beginning with MSA, product and process improvements may be realized. Inspection difficulties between suppliers and customers may be resolved. And yes, it may even lead to the commercialization of a new product for your company. The next time you participate in a measurement system study, think of the possibilities beyond checking the “done” box on the PPAP.

Charles W. (Wes) Shelton is an ASQ senior member and education chair of the Inspection Division.
Looking for a reprint of this article?
From high-res PDFs to custom plaques, order your copy today!