Speaking of Quality | Navin S. Dedhia
Quality Inspector in Quality 4.0
Quality 4.0 does not focus exclusively on the technology, but rather on the improvement in culture, collaboration, competencies, and training.
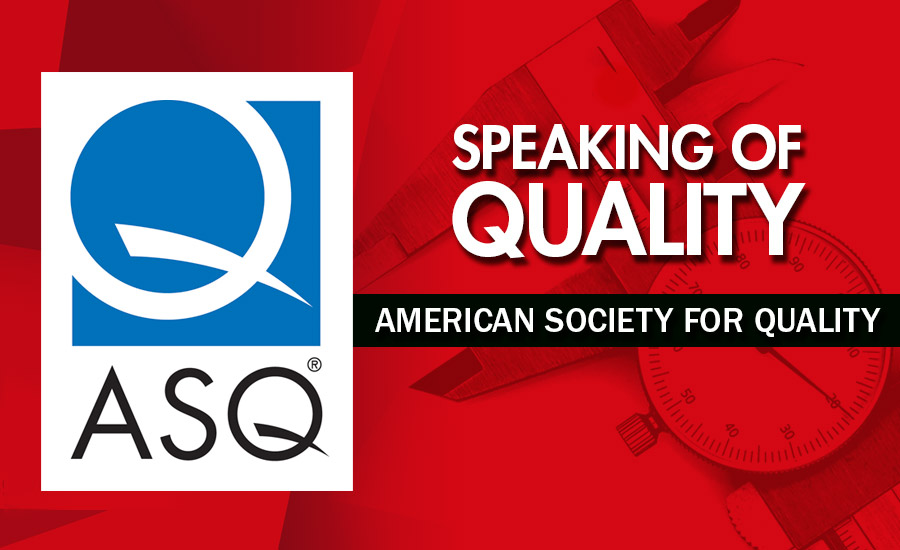
Industry 4.0 and resulting Quality 4.0 are driven by the exponential growth of disruptive technologies and the changes these technologies are bringing to the workplace. Quality 4.0 connects the inspector to machines and machines to data. Inspectors who have an attitude of never stop learning will gladly embrace the change.
The fourth industrial revolution is the move towards digitization including automation, robotics, and artificial intelligence. Quality 4.0 is not a trend, but a reminder that performance excellence depends on how well technology is being adapted, changed, and transformed.
Inspector Role
The emergence of smart factories has placed a high demand for qualified and skilled inspectors.
The inspector is the person perhaps most integrally involved with day-to-day activities intended to ensure products and services meet customer expectations. The inspector identifies defects, finds deviations from set specifications, evaluates hardware documentation, performs laboratory procedures, inspects products, measures process performance, records data and prepares reports.
The inspector’s role is viewed as an advocate, partner, collaborator, contributor, counselor, standard enforcer, objective auditor, watchdog, data collector, data analyst, and team member. However, some view the inspector role negatively as adversarial, a rubber stamper, informer, nitpicker, whimsical critic, spy and fortune teller.
Inspectors are individuals who
- Are professionals in their own right
- Have chosen their field of specialty
- Know their strengths and limitations
- Have visible standards of excellence
- Have a never-ending desire to learn
- Are teachers, mentors and coaches
- Know their own worth and value
- Use SWOT (Strength, Weakness, Opportunity & Threat) tool
- Are prevention oriented
- Always promote teamwork
Inspection includes activities such as measuring, examining, observing, testing, evaluating one or more characteristics of a product or service or comparing with specified requirements to determine status (audit).
Quality Inspector Skills
ASQ Inspection Division supports ASQ Certified Quality Inspector (CQI) and ASQ Certified Quality Technician (CQT) certification examination. The Inspection Division sets examination requirements, and test questions and evaluation criteria. From time to time, the division addresses changes in the Body of Knowledge requirements.
ASQ Certified Quality Inspector – CQI certification is meant to evaluate inspector knowledge and skills. The inspector is required to be proficient in the following subjects, called Body of Knowledge, which are:
- Technical mathematics - Requiring broad overview of technical mathematics in making the report
- Metrology - Capable of identifying, selecting, and using the right metrology gages and instruments
- Inspection and Tests - Application of inspection processes using GD&T and traceability, as well as implementing testing methods
- Quality Assurance - Optimize quality techniques using basic statistics
- Audits - Knowledge of comprehensive overview of quality audits, quality tools/techniques, and problem-solving
The ideal candidate should possess an in-depth knowledge of applicable quality standards. The inspector is required to understand and apply a variety of tools, techniques and methodologies when inspecting the product and thinking to improve the operation.
Quality 4.0 Industry Skills
The emergence of smart factories has placed a high demand for qualified and skilled inspectors. Inspectors should have general knowledge and application of developing technologies such as artificial intelligence and machine learning, big data, cloud computing, augmented and virtual reality, new materials, 3D printing, and the Internet of Things (IoT).
Inspectors must be capable of analyzing large amount of data to be able to predict possible failures and adapt to conditions in real time. Additionally, creativity, flexibility, analytical thinking, knowledge of spreadsheets (Excel), basic statistical knowledge, problem solving ability, and willingness to learn new things will be an asset.
In times past, inspection was at the end of a process. In quality 4.0 industry, inspection is built into the process. Inspection is in the line and a part of the process. The result is error detection at an early point.
Future quality inspectors will have to acquire skills to monitor, control, improve and manage vast amount of data. Quality inspectors must understand and acquire knowledge of:
- Automated tools, systems, process and new materials
- Research & Development to understand future processes and products
- Engineering, operations using smart tools
- Internal and external customer and their requirements
- Applicable quality standards
- Benefits of automation and robotics
- Capability to program and manage the technology.
It will be beneficial to acquire knowledge of noncontact inspection methods, X-ray technology, contactless dimensional inspection measuring instruments, coordinate measuring machines (CMMs) and computer-aided inspection in smart factories.
Inspectors are the greatest assets. Social, political, economic, and technical forces shape the future of inspectors. Pushing technology because it is the latest fad or to beat competition instead of pulling technology based on the opportunity may not give enough time or training for inspectors. Undefined digital strategy will create confusion. When leadership is not supportive, inspectors must live with outdated systems and infrastructure along with fragmented quality data.
In industry 4.0, inspectors can monitor processes and collect data in real-time and apply analytics to predict quality issues and maintenance needs. Inspectors can improve quality in various ways in factories using digital technologies that are accompanied by smarter practices and procedures.
Looking for a reprint of this article?
From high-res PDFs to custom plaques, order your copy today!