Computed Tomography
Advanced Applications of X-ray Computed Tomography (CT) in Aerospace
As high-energy systems become more powerful and AI-driven analysis becomes more sophisticated, CT will continue to play a crucial role in ensuring the safety, reliability, and performance of aerospace components.

CT Metrology on a Turbine Blade. Image Source: North Star Imaging
X-ray computed tomography (CT) has transformed numerous industries by offering nondestructive, three-dimensional insights into the inner structure of components.
In the aerospace sector, where safety, precision, and quality are paramount and in the spotlight these days, CT technology has become an indispensable tool. From early defect detection in manufacturing to maintenance inspections of complex assemblies, X-ray CT is integral to both quality assurance and research and development.
As technology continues to evolve, high-energy CT is pushing the boundaries of what is possible, allowing for deeper penetration of dense materials and more detailed imaging.
Here we will explore the technological advances, methods, and trends in X-ray CT applications in aerospace. By discussing high-energy CT, developments in data processing, and the evolving methods of inspection, we will provide an overview and understanding of how CT is shaping the aerospace industry today.
Understanding the Basics: How X-ray CT Works
At its core, X-ray CT uses a series of X-ray projections taken from different angles to create a detailed 3D representation of an object. In traditional radiography, X-rays pass through an object and produce a 2D image. However, this method has limitations in terms of revealing overlapping structures and hidden features. CT addresses these limitations by generating cross-sectional images (or slices) that can be compiled into a detailed 3D model of the object under investigation. This allows engineers and inspectors to visualize and analyze internal structures that would otherwise remain hidden.
Key Aerospace Applications of X-ray CT
- Component and Assembly Inspection: In aerospace, components such as turbine blades, composite structures, and even complete engine assemblies are subjected to stringent inspection protocols to ensure they meet design and safety standards. X-ray CT allows for the detection of internal defects such as cracks, voids, delaminations, and foreign materials within components without the need for destructive testing. This makes CT invaluable in verifying the integrity of critical parts both during production and throughout the service life of aircraft.
- Material Analysis: Aerospace components are often made of advanced materials such as titanium alloys, carbon fiber composites, and ceramics. These materials require meticulous evaluation to ensure their properties meet performance specifications under various stresses. X-ray CT provides detailed imaging that helps in understanding material behavior under load, offering insights into potential failure modes. CT scans can also be used to evaluate the porosity of composite materials, essential in maintaining structural integrity and performance.
- Additive Manufacturing (AM) Inspection: The aerospace industry has embraced additive manufacturing, or 3D printing, for creating complex components that are lightweight yet strong. However, the layered manufacturing process can introduce defects like incomplete fusion or residual stress points. X-ray CT provides the ability to inspect these components layer by layer, ensuring that internal defects are detected earlier, which is crucial for parts used in critical aerospace applications.
The Rise of High-Energy CT in Aerospace
While traditional X-ray CT systems are effective for many applications, they often struggle with denser materials such as metals or large assemblies typical in aerospace. This is where high-energy CT systems, particularly those operating at 9MeV, come into play. These systems have the power to penetrate thicker and denser objects, making them ideal for inspecting complete engine assemblies, large composite structures, and even aircraft fuselage sections.
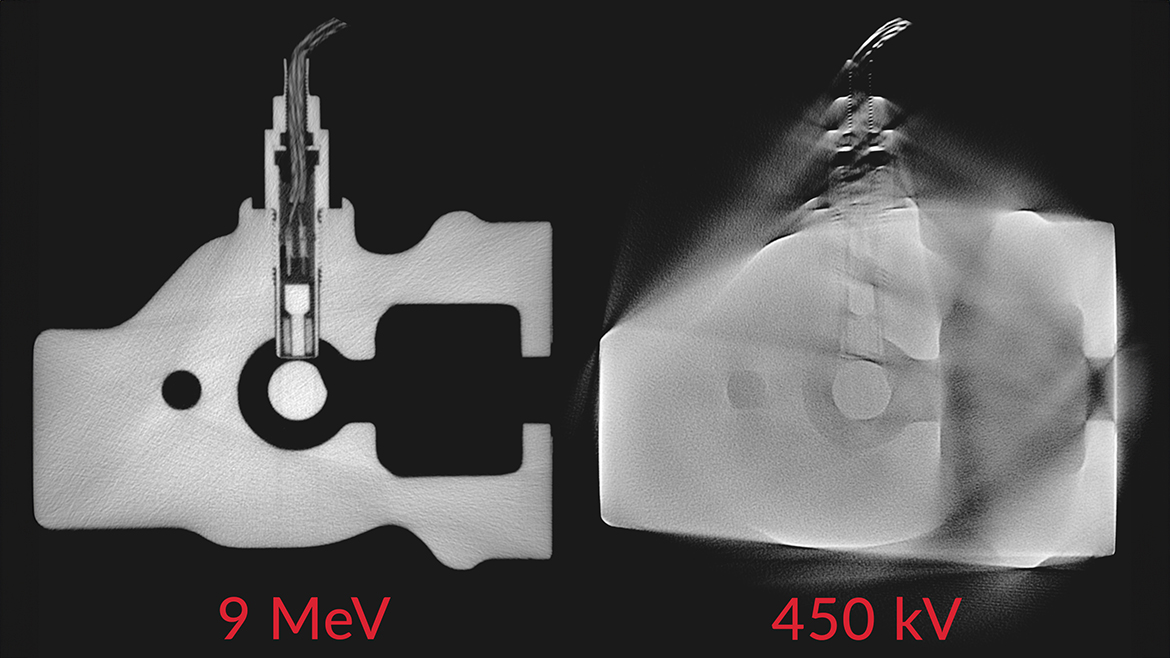
High-energy CT has several advantages:
- Penetration of Dense Materials: A 9MeV CT system can easily penetrate high-density materials like steel and titanium, providing clear and detailed images of internal structures that would be impossible to visualize with lower-energy systems.
- Large Field of View: High-energy CT systems are capable of scanning larger objects without sacrificing resolution. This is essential when inspecting larger aerospace components, such as engine parts, where high precision is needed over a wide area.
- Improved Speed and Efficiency: High-energy CT scans can often be completed faster than their lower-energy counterparts due to their increased penetrating power. This efficiency is particularly beneficial in aerospace, where minimizing downtime is critical.
There are high energy systems (6-9MeV) CT systems designed specifically for large-scale industrial inspections. These high-energy CT solutions are used in aerospace for inspecting high-density components like turbine blades and aircraft engines, where even the smallest defect could lead to catastrophic failure.

Advances in Data Processing and Software
As the capabilities of X-ray CT hardware have improved, so too have the data processing algorithms and software that support it. Modern CT systems can generate vast amounts of data, often reaching gigabytes or terabytes per scan. Processing this data efficiently and extracting meaningful information requires powerful software.
Recent developments in artificial intelligence (AI) and machine learning (ML) are revolutionizing how CT data is interpreted. These technologies can automatically detect defects, classify materials, and even predict potential failure points based on historical data. The integration of AI into CT analysis can reduce the time required for inspection, minimize human error, and provide more accurate and repeatable results.
For example, AI-driven algorithms can identify patterns in CT images that may be too subtle for the human eye to detect. This is particularly important in aerospace, where even a minor defect in a critical component could compromise safety. By automating first line of defense defect detection and classification, AI-enhanced CT systems offer a more robust inspection process, ensuring that defects are identified and addressed before they become a problem.
Digital Twin Trends in X-ray CT for Aerospace
Digital twins, or virtual replicas of physical objects, are becoming increasingly important in aerospace. CT plays a critical role in creating these digital twins by providing the detailed 3D imaging needed to accurately represent physical components in a virtual environment. Once a digital twin is created, engineers can simulate various scenarios, such as stress tests or thermal cycling, to predict how the component will behave under different conditions. This allows for more efficient design optimization and testing, reducing the need for physical prototypes.

Reverse Engineering
Reverse engineering deconstructs an object through a nondestructive technique to analyze its internal structure, design and functionality. It is a vital process used in aerospace as it helps engineers and manufacturers improve their production methods and existing designs of products. Scientists can conduct reverse engineering through several different techniques, but CT is favorable because of their non-invasive, powerful inspection methods. Reverse engineering is not necessarily carried out to duplicate the part, but for analytical and testing purposes. It can be used for replicating worn parts or converting physical models to digital ones. This method is invaluable for analyzing legacy parts where original manufacturing data may no longer be available or where the original manufacturer no longer produces the parts. Using CT scans, engineers can accurately capture the internal and external geometry of components, enabling them to recreate or modify designs for improved durability, performance, and compatibility with modern systems. Additionally, reverse engineering through CT can be used to optimize existing designs, ensuring that parts function more efficiently within their structural systems. This approach is not only crucial for life-cycle management of aerospace components but also for innovation and improvement in the aerospace industry.
Future Directions
The future of X-ray CT in aerospace is promising, with continued advancements in both hardware and software. As high-energy systems become more powerful and AI-driven analysis becomes more sophisticated, CT will continue to play a crucial role in ensuring the safety, reliability, and performance of aerospace components. Furthermore, the integration of CT with other NDT methods and the adoption of digital twin technology will provide even greater insights into the inner workings of aerospace systems.
These advancements are not only improving the quality of aerospace components but are also contributing to the overall safety and reliability of modern aircraft.
By staying at the forefront of CT technology, aerospace companies can ensure that their products meet the highest standards of quality and safety, helping to secure the future of air travel.
Looking for a reprint of this article?
From high-res PDFs to custom plaques, order your copy today!