Test & Inspection
Energy Costs, EV Growth Drive Changes in Leak Testing Methods
The scope of leak testing applications continues to expand beyond traditional industries.
.jpg?1738009418)
Labthink’s brand new automated vial batch leak tester. Leaking vials are automatically segregated for further inspection. Image courtesy of LabThink
Leak testing is changing quickly as manufacturers face new challenges in electric vehicle production, sustainable practices, and automated testing solutions. These changes are reshaping how companies approach quality control across industries, from automotive to HVAC and medical devices.
New Markets Drive Innovation
The emergence of electric vehicles and hydrogen technology is creating new demand for specialized leak testing solutions. Industry leaders report a significant uptick in hydrogen-related testing needs across multiple sectors.
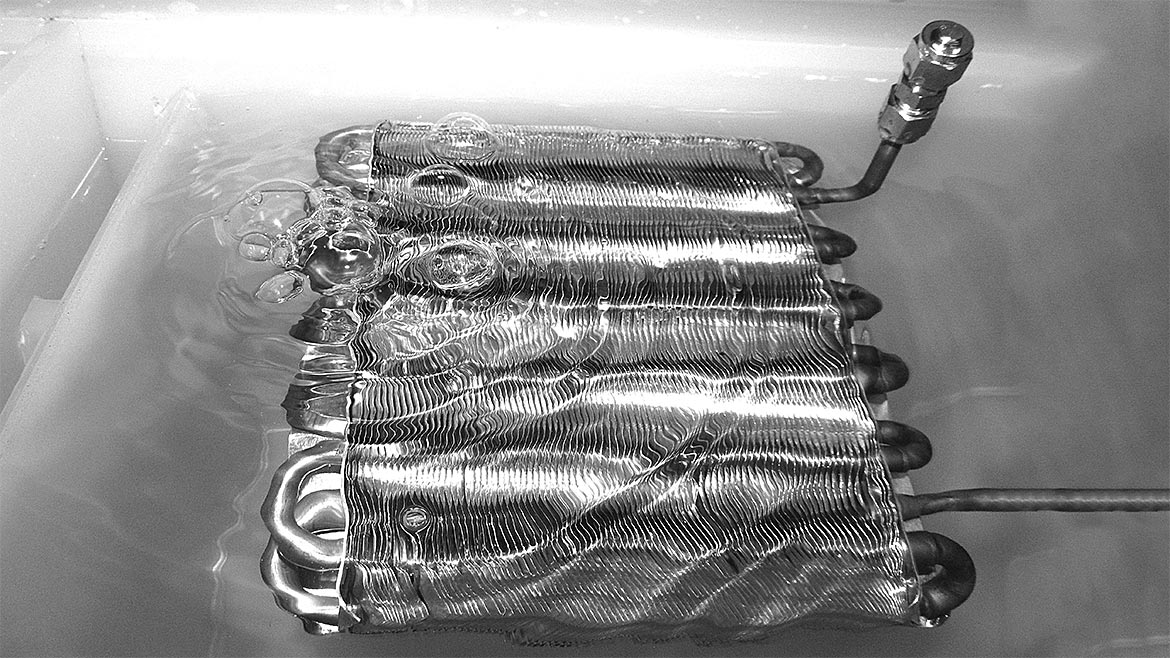
"The hydrogen market has really taken off. Fuel cells, storage and distribution, and transportation are just a few of the projects we’ve been involved in," says John McLaren, business development manager for leak detection at Pfeiffer Vacuum. "Obviously, leak detection is a critical quality control measure in the industry."
The scope of leak testing applications continues to expand beyond traditional industries. As manufacturers introduce increasingly complex products across sectors, testing requirements have evolved to meet novel challenges.
"In a word: variety," McLaren says. "It seems like there’s an ever-increasing need for products to be leak tested. We’ve tested everything from mattress temperature regulation systems to heart pacemakers to carbon capture systems. Always something new."
Electric vehicle safety presents particular challenges. As the automotive industry shifts toward electric vehicle production, manufacturers must ensure the integrity of battery components to prevent potentially hazardous failures. "The trend toward more electric vehicles on the road is significantly growing, but there are valid safety concerns about what can happen if their lithium-ion batteries leak. Pfeiffer helps manufacturers by providing them with proven methodologies that ensure their batteries meet safety requirements," McLaren explains.
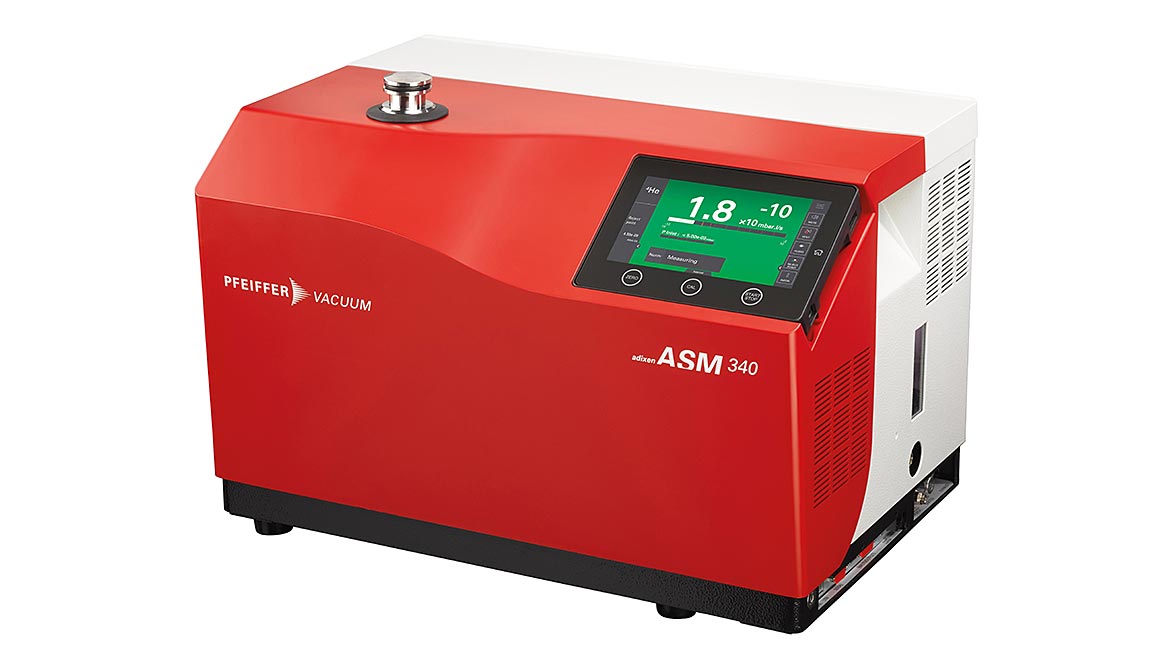
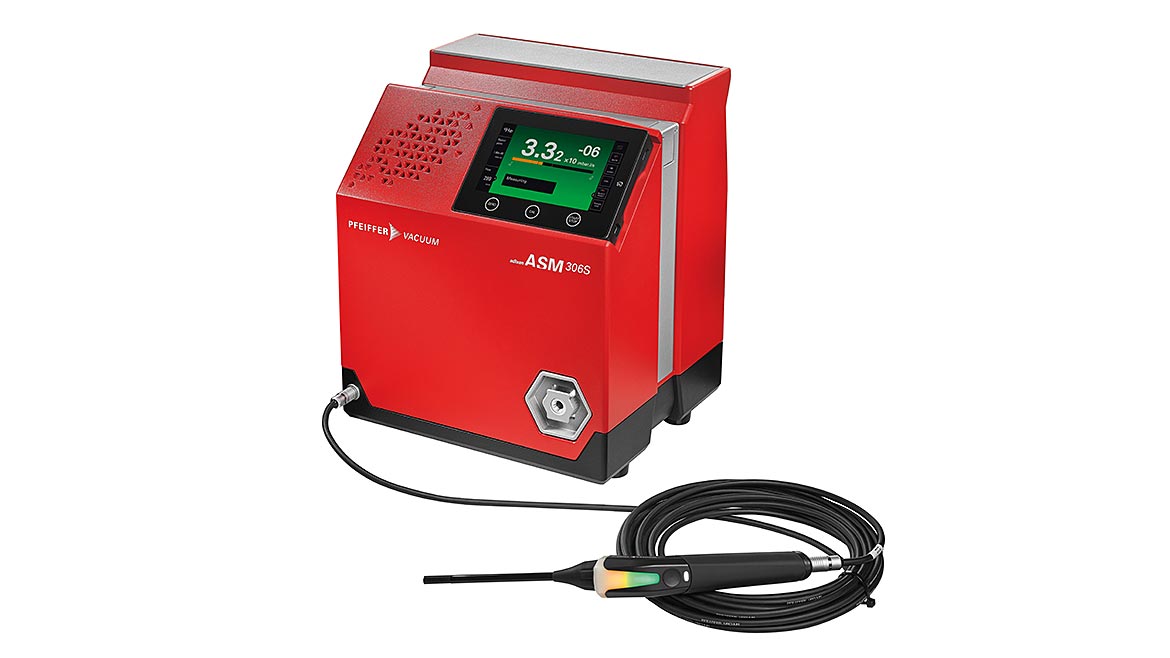
In the HVAC sector, robotics are transforming testing processes. The complexity of modern HVAC systems, with their numerous connection points and seals, demands increasingly sophisticated testing methods. "In HVAC, emphasis is on robotic leak testing using automated sniffer probes. HVAC products have an exceptional number of joints, and ensuring each is leak tested is critical," says Thomas Parker, automotive leak testing sales manager at INFICON. "We see an increase in the use of forming gas for sniffing applications."
Standards Evolution and Compliance Challenges
The rapid pace of technological change has created gaps in industry standards, particularly for newer technologies. This gap is especially noticeable in the electric vehicle sector, where safety standards haven’t kept pace with technological advancement. "While strict standards for fuel vapor emissions and air bag inflators exist, they do not exist for the traction-battery industry in North America," Parker says. "Our company, INFICON, authored three SAE papers that examined the relationship between materials and leak rates beyond typical IP (Ingress Protection) ratings, which we find mostly insufficient. As water vapor itself is a hazard, SAE has been working on standards for leak tightness for over 18 months. The same will apply to sensor technologies for autonomous driving."
Gordon Splete, product manager and marketing at Cincinnati Test Systems, identifies two significant transitions in leak rate specifications. First, the HVAC/R industry faces stricter environmental requirements. "The HVAC/R industry is lowering their leak rates to accommodate the shift from past Greenhouse gases to more environmentally friendly freons," he says.
These lower leak rates present technical challenges. "Different trace gas testing techniques that are more complex than simple open air sniff testing is necessary to measure leak rates that are lower than the background gases in the environment," Splete explains. "With this change the trend is that Cincinnati Test Systems is helping coach manufacturers to understand the best technology for meeting their test specifications and budgets for the required production rates to keep their lines balanced."
The second transition involves electrical components. As electronics become more prevalent in challenging environments, manufacturers face increasing pressure to ensure reliable water protection. "The Electrical Industry is using IP67 as their specification for no-water ingress. This specification is an attribute test identifying that when a sealed electrical component is submerged 1 meter underwater for 30 minutes it does not have visible water ingress," Splete says. "The need is that companies need to convert this physical attribute test into an automated measurable test."
Martin Bryant, director of sales at Labthink International Inc., notes that while standard compliance itself isn’t the primary challenge, market demands create pressure. "I think that the standards themselves (such as ASTM and ISO) are not so difficult to comply with. The challenges lie more in the demands and expectations of the end use markets for tighter and tighter performance specifications as reflected in admissible leak rates," he says.
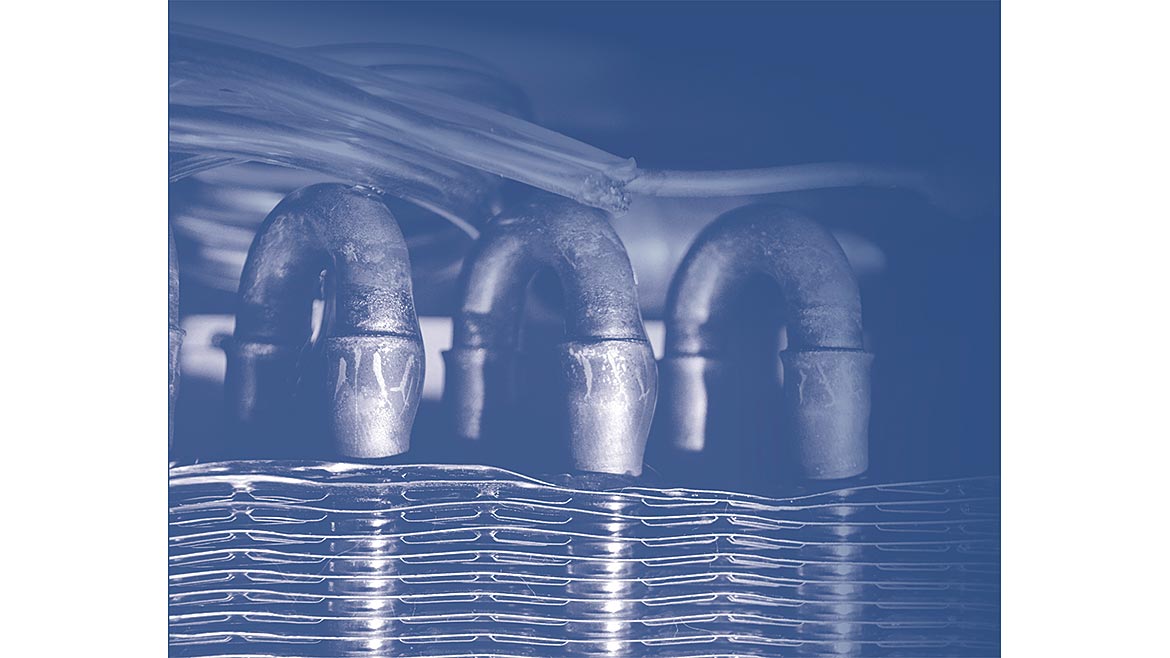
Sustainability’s Growing Impact
Environmental considerations are increasingly influencing leak testing methods and materials. As companies shift toward more sustainable packaging options, these eco-friendly alternatives often bring new testing complexities. "New materials introduced in pursuit of more sustainable solutions for packaging materials may present challenges for leak testing such as porosity and capacity for effective heat sealing," Bryant explains. "Inconsistency in these two critical areas of package design present huge challenges for leak testing and the provision of reliable data."
Rising energy costs are pushing manufacturers to find more efficient testing methods. Companies are exploring new ways to reduce both energy use and expensive test gases while maintaining quality standards. "Both energy and test gasses are costly. Accumulation leak testing offers a lower energy consumption alternative. Diluting helium used for testing decreases cost, but can alter testing times. Our EcoBoost allows complex helium chamber leak testing to be accomplished at line speeds while permitting less powerful vacuum pumps which saves energy costs," Parker says.
Beyond the testing process itself, even small leaks can significantly impact a facility’s overall energy consumption and operating costs. McLaren emphasizes the economic implications of leak testing efficiency: "We’re addressing customer concerns about what leaks cost them in terms of energy consumption. Whether you’re creating a vacuum or pressurizing something, the pumps and compressors you use to do that consume energy, in some cases a lot! We can show customers how reducing leaks can save on utility costs and improve their process efficiency."
Helium conservation has become another priority. "When testing using trace gas technologies, a non-reactive gas is used to pressurize parts under test, gases like Helium which when released into the atmosphere is not recoverable with any cost-effective measures," Splete says. "Many manufacturers are finding that implementing a Helium Reclaim system into their testing process is saving money and reducing the consumption of the world’s Helium supply."
Automation and AI Integration
The COVID-19 pandemic accelerated automation trends in leak testing. "Beginning with COVID-19, discussions of (sniffer) leak tests without operator involvement grew," Parker notes. "The necessity for greater certainty that components have been tested to an appropriate level of leak tightness — that awareness is growing. However, we see little to no true AI, today, at our business level."
The adoption of automation varies by sector. While automotive manufacturers have embraced automated testing systems for high-volume production lines, research and quality assurance labs often require more flexible, manually operated equipment.
However, manufacturers increasingly seek connected solutions. The drive toward Industry 4.0 and data-driven decision making has created demand for testing systems that can integrate with broader quality management networks. "Customers routinely ask us to deliver a customized solution that simplifies and mistake-proofs their test," McLaren says. "Along with a higher level of automation they’re seeking more connectivity options (ethernet, mobile apps, etc.) and data collection for trend analysis."
Future Developments
Looking ahead, experts anticipate continued innovation in leak testing methods and applications. Vision systems will play an increasingly important role in automated testing across industries. "We expect, more and more, vision systems to deliver even more robust automated sniffer leak testing in multiple industries, greater use of diluted helium and more options to use alternative tracer gases other than helium," Parker says. Advances in efficiency features are expected to improve line speeds and reduce test-gas contamination while enabling comprehensive component testing.
While breakthrough technologies may not be imminent, machine learning could help manufacturers optimize their existing testing processes. Bryant sees potential for AI applications. "I don’t foresee any significant technology innovations but would not be surprised to see more and more use of AI in the role of data analysis and the improvement of test cycle times through predictive methods," he says.
As products become more complex and miniaturized, testing requirements must evolve accordingly. "Manufacturers are always pushing for tighter leak rates," says McLaren, noting that smaller devices have lower contamination tolerances. He predicts the industry will see increased demand for customized testing solutions to meet these precise requirements. "As devices get smaller, the amount of contamination they can tolerate before failure gets smaller," he says.
The electric vehicle sector will continue driving innovation in leak testing methods. As EV production scales up globally, manufacturers face the dual challenge of maintaining quality while increasing testing speed. Splete predicts that the industry will need to develop more efficient, cost-effective ways to test high volumes of battery cells. He also expects predictive testing methods to gain traction as artificial intelligence capabilities advance and gain broader acceptance in manufacturing.
The leak testing industry continues to evolve as manufacturers face new challenges. Success will depend on finding faster, more efficient testing methods while maintaining high quality standards and meeting environmental goals.
Looking for a reprint of this article?
From high-res PDFs to custom plaques, order your copy today!